Why Use Compressed Air Anyway?
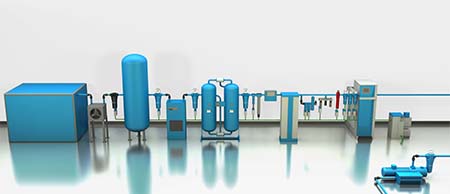
Compressed air is often referred to as the “fourth utility” in industrial operations, alongside water, electricity, and gas. Its versatility makes it essential for powering tools, controlling automation systems, and maintaining manufacturing processes. From running pneumatic tools in automotive assembly lines to ensuring precise control in food and beverage production, compressed air enables efficiency, consistency, … Why Use Compressed Air Anyway?